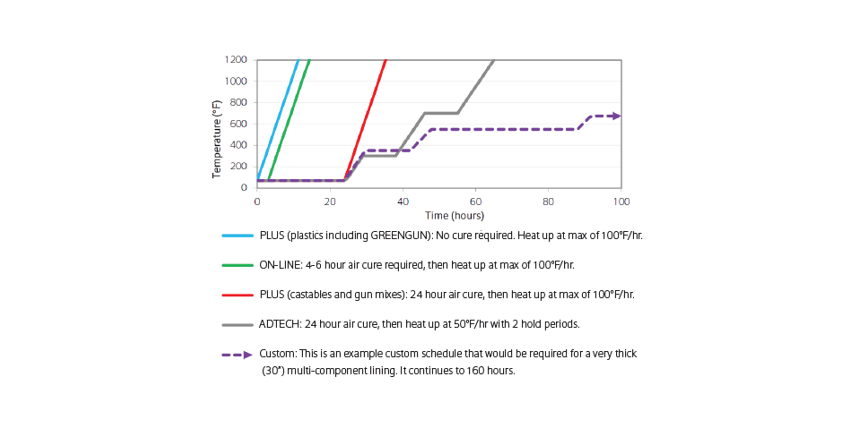
We find ourselves in the cold-weather-installations time of the year. The proper installation of refractory castables includes mixing, placing, curing, and drying. At HarbisonWalker International, we consider every detail when it comes to developing best practices for all phases of refractory installation.
Installation
Careful attention must be paid when adding water and mixing castable materials. Excessive amounts of water can negatively impact the refractory – lower strength, longer set time, and more water that must be removed during dryout.
Lower strength and excessive water to remove can make for a higher-risk dryout. Use the proper water target, which can be found on the product datasheet.
Curing
The curing process begins when the water is added to the castable and begins to react with the cement. The process ends when the material is hard and has achieved its final set. Curing behavior is directly impacted by both the ambient and castable temperature. The ideal curing temperature range is between 70°F and 90°F. Curing at temperatures below 70°F can produce negative effects: lower strength, lower permeability, and extended curing time.
Conversely, excessively hot conditions can cause the material to set too quickly, resulting in poor densification or even render the material unable to be put in place.
Temperature control
Store material and equipment in a controlled atmosphere. Cold refractory material can take several days to stabilize to the desired temperature. Use heaters in cold conditions to apply heat to the vessel or space around the curing refractory. Heaters should not be pointed directly at refractory surfaces.
Storage and mixing temperatures of refractories are paramount to achieving desired installation characteristics.
Failure to properly mix, place, and cure refractory materials along with using improper dryout schedules or practices can result in severe spalling (as shown in photo above).
Water Removal
After the castable has been installed and hardened, there are two types of water remaining: physical water and chemical water. Both must be removed before the refractory material can be used in service.
Physical Water: enables the castable to flow, and is also referred to as “free water” because it sits in the pores of the castable and is not bound by any hydrate phases.
Chemical Water: chemically combined water tied up in various cement hydrate phases.
Heat needs to be applied to remove both types of water. The physical and chemical water is released at certain critical temperatures during the dryout which are as follows:
- Removal of free water: 212°F (100°C)
- Dehydration of major cement phases: 440°F (227°C), 530°F (277°C), and 1020°F (549°C)
All water must be removed in a controlled manner and dryout schedules should pay attention to these critical temperatures.
When water turns to steam there is a volume expansion of approximately 1,600 times. This increase in volume causes high pressures within the lining. At each critical temperature there is a high potential for developing internal pressures that could exceed the strength of the refractory castable and cause the material to spall.
HWI Dryout Schedules
The dryout process is usually the last step before a refractory castable lining is put into service. The recommended practices of HWI must be followed for each mixing, placing, curing, and dryout step in order to achieve the optimum lining. The dryout should not be compromised because improper procedure may lead to microcracks, shorter life, or a steam explosion.
HWI has developed standard dryout schedules to be applied in many circumstances. These are designated in the product name with the suffix PLUS, ON-LINE®, or ADTECH®. Each are described in the graph below. HWI standard schedules can be used with single component linings that are 9 inches thick or less.
Excessively thick and multi-component linings must be evaluated on a case-by-case basis. HWI should be consulted for the proper dryout schedule in these scenarios. Slower heating rates, additional holds, and other non-refractory variables (such as weep holes and wicking practice) may be required.
The information in this article is for informational purposes. Every project can be unique. For product and application suggestions, please be sure to reference HWI product information and reach out to your sales representative or HWI application specialist for suggestions for your project.
About HWI, A member of Calderys
HWI is one of the leading suppliers of refractory products and services in the United States, with a history that spans more than 150 years. It is part of Calderys and is the brand for the Americas region of the Group. HWI operates an extensive network of manufacturing sites and distribution centers across the Americas, along with the largest refractory industry research facility in North America. Serving virtually every major industry that requires refractory solutions to enhance production and protect assets, HWI is consistently recognized for its talented experts, industry firsts, and intensely driven excellence.
For more information, visit https://thinkhwi.com