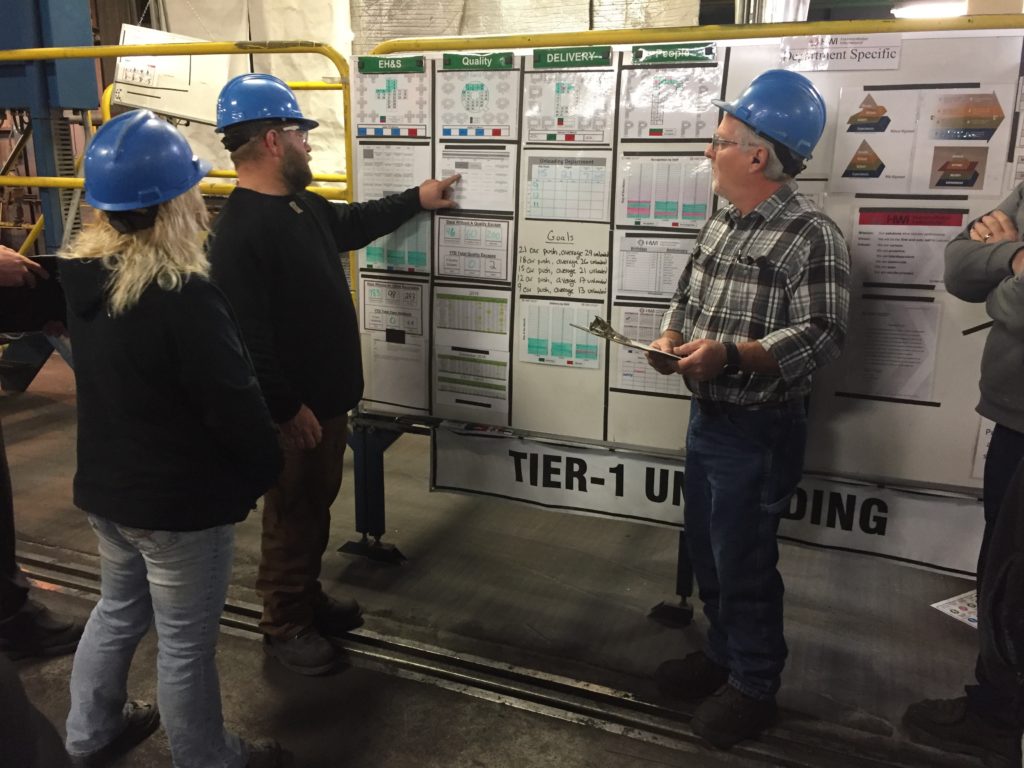
Continuous improvement is at the forefront of everyday operations at HWI, and ensuring the proper people and processes are in place to guarantee HWI continues to grow and adapt to our customers’ changing needs has been a vital part of making HWI the first call for industry.
In a world that is constantly changing, our customers’ needs are always evolving. To stay competitive, HWI needs to keep pace with that evolution. Sustainable evolution that builds operational excellence within our business requires a governance system as well as a commitment from each employee to uphold that commitment as a core value.
HBS is that system. It is the way everyone at HWI works, and it provides the framework, tools, and skills to help each employee be a professional problem solver and drive sustainable improvement to deliver for our customers every day. HBS combines several different sets of principles rooted in Lean and Six Sigma to create a customized tool set for our business and our employees.
Originally implemented back in 2015, Harbison Business Systems, or HBS, is a critical component of every HWI employees’ daily life, providing each with a solid framework to ensure HWI continues to grow and evolve sustainably. HBS ties together how our employees lead and communicate, solve problems, plan strategically and measure processes and their performance while serving our customers as efficiently as possible.
The focus is on three pillars of the HBS House of Lean: Just in Time Flow, Empowered Employees, and Waste Elimination. After implementation, HBS significantly changed how our employees “acted”, “worked”, “lead”, and “thought”.
During the initial HBS rollout back in 2015, the primary focus was on the Integrated Supply Chain, more specifically those at the manufacturing level.
Procurement, Quality, Project Management, the Advanced Technology and Research Center and our Commercial group were all among the first groups at HWI to be Fireclay Certified, the second tier of excellence for HBS.
The initial phase included deployment of some very basic or foundational lean elements, including 5S, Tiered Accountability, Visual Management, Leader Standard Work, Rapid Problem Solving and the Waste Identification.
While HBS was successful following its initial implementation, we determined there was a need to refresh the organization. In 2020, HBS was implemented across our entire company with a different approach, ensuring that every group in our interconnected value chain continues to evolve at a similar pace.
Successful implementation of HBS is measured in four tiers ranging from Foundational (Business Readiness) to Chrome (Business Excellence). As of this year, the entire organization has achieved the third-tier Bauxite level of excellence or better, mastering the key issues of driving continuous improvement and eliminating waste through Knowledge Sharing, Advanced Problem Solving, Kaizen and Waste Elimination.
Combining our HBS system with HWI’s organization-wide training and development resources has identified and created impactful programs that continue to drive positive change across the organization.
About HWI, A member of Calderys
HWI is one of the leading suppliers of refractory products and services in the United States, with a history that spans more than 150 years. It is part of Calderys and is the brand for the Americas region of the Group. HWI operates an extensive network of manufacturing sites and distribution centers across the Americas, along with the largest refractory industry research facility in North America. Serving virtually every major industry that requires refractory solutions to enhance production and protect assets, HWI is consistently recognized for its talented experts, industry firsts, and intensely driven excellence.
For more information, visit https://thinkhwi.com